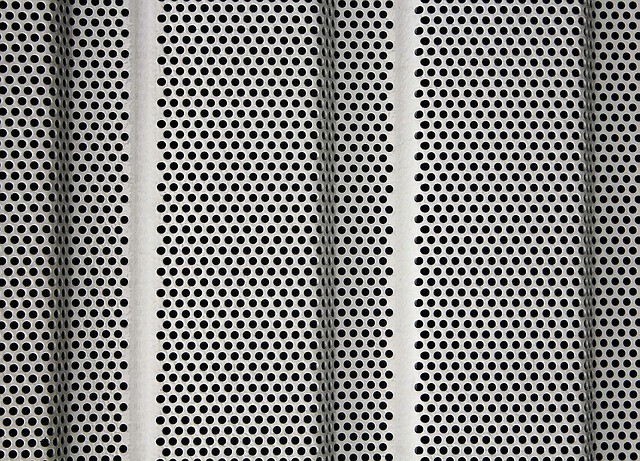
Table of Contents
So, you’re starting a massive new project with your company. You’ve done your research. You hired a contractor who hired a company to punch out your metal for prototyping. But, then you get a call and they’re unable to complete the job.
This is a big problem. Jobs are on the line! And now your project is facing major delays. With New Age Metal Fabricating, you don’t have to worry about that. We’re backed by the big guys, but have the touch of a small business. When working with us, you’ll have one point of contact in charge of your job. And we’ll use the top technology to make sure your project is completed quickly, efficiently, and perfectly.
Working with NAMF
Custom machining services involve a range of tools and applications, each with its own features and characteristics.
This means that no matter the project you have in mind, there is a type of custom machining technology best suited to it. With our modern technology, your project will be quick, efficient, and precise. Because most of our work is suitable for mass production, we commonly use sheet metal punching.
A punch press is the machine used to cut holes in materials. Often, this machine is small and hand-operated. But, it can also be large, CNC-operated with a multi-station turret.
For small jobs or operations such as prototypes, tooling costs can run very high. One way of keeping costs down is through the use of a turret punch. When tooling with a turret punch, you can create holes of varying sizes, straight edges, commonly-used notches or mounting holes.
By using a large number of strokes and with several different tools, a turret press can manufacture a wide array of parts without having to make a specialized press tool for that task. It saves you time and money. This is used in rapid prototyping or for low volume production jobs that can begin without tooling delays.
What is Sheet Metal Punching?
You may be curious about how sheet metal punching works. Essentially, this is when a large machine punches a hole in a sheet of metal. This is a three-step process.
- The sheet metal is secured on top of a die. The punch is prepared on top of the sheet.
- The punch is then pressed into the sheet metal. Because of the die underneath, the sheet is penetrated by the punch.
- The process is repeated from step 1. All scrap metal is collected.
What Should You Consider?
While the steps are simple, in practice, the sheet metal punching process can be complicated.
There are many things to consider:
- How large is your project?
- How thick is the metal you need to use?
- How much force will the punch need to exert?
- Will the punch be working well?
- How complex is the size and shape you are punching?
- How repetitive are my requirements?
- Do I want to deal with multiple manufacturers or a one-stop, specialist?
Our punching process prioritizes your needs. Our machines are able to punch holes quickly, consistency, and economically.
Why should this matter to you? It means your project will be completed on time and to your exact specifications. Our competitors are unable to match our quality or speed.
What Equipment Do We Use?
We primarily use computer numerical controlled (or CNC) punch. This means that we are ready and able to help you create your project to your exact specifications.
Typically, a turret punch has up to 60 tools located in the “turret,” which is rotated to bring the proper tool into position for use in the current sheet metal punching process. Simple shapes such as circles, squares, or hexagons are cut directly from the sheet. However, more complex shapes can be cut out as well. This is done by making rounded or square cuts around the perimeter.
Every press tool requires a matching tool and die set. There are two corresponding turrets, one above and one below the bed, for punch and die. These turrets must rotate and be completely synchronized and aligned.
A punch is less flexible than a laser for cutting complex shapes, but it works better for repetitive shapes. Some units will combine both laser and punch features in one machine. For the most part, turret punches are CNC, with automatic positioning of the metal sheet.
Turret punches can operate faster per stroke than a heavier tool press. While CNC punches are less flexible than laser cutting tools overall, they are faster at creating repetitive shapes.
Both New Age Metal Fabricating and New Age Precision Manufacturing operate Amada CNC punch presses, which can accommodate sheet sizes up to 50×78. We utilize is the Amada Vipros 357 Queen 33 Ton CNC Turret Punch Press and the Amada Pega NC Punch 345Q.
Why Choose New Age Metal Fabricating
As custom steel fabricators, our one-stop-shop with products delivered on time and high-quality parts is only the beginning. Our prices are always competitive and our expertise is known throughout the industry.
Our New Age Companies are always striving for excellence in everything we do. We have the expertise to provide you with complete manufacturing services for all your sheet metal punching and metal fabrication needs.
We don’t want you to be jerked around by multiple companies and several middlemen. At NAMF, you’ll have one point of contact. You can think of them as your project manager.
They’ll guide you through the entire mental punching system. They’ll make sure you feel confident in our process and your results.
Advantages of Choosing New Age Metal Fabrication for all your CNC Cutting Services:
- We are a single-source supplier for all of your sheet metal punching, precision manufactured and dip-brazed products.
- We offer you complete and turnkey solutions for all of your material purchasing needs.
- We are in control of each step of your product from start to finish.
- For each product or design, you will have only one point of contact.
- We save you money and time by eliminating the need for multiple suppliers.
- We provide you with a finished product that is ready for your production line.
- We are approved by the BAE and Lockheed Martin to supply dip-brazed, chemical film, welded, and painted components.
- We have NAVSEA approval to dip-braze and weld to Navy specifications.
- We handle all customer requests quickly.
- Our engineering team has decades of experience to help your final product designs reach fruition.
Contact us today to discuss your company’s vision and your upcoming projects.
No matter what you need – a supplier for products in use or innovative new answers to streamline your production – we have the answers you’ve been seeking. From custom CNC cutting services to a painted or dip-brazed finished product, our New Age Metal Fabricating solutions are here to help you right now.